Impulse-EV Technology
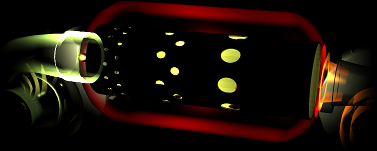
The 400hp from the twin micro-turbine generator powerstation supply the wheel motors directly.
They also charge a supercapacitor pack to provide the megawatt boost to accelerate you to the horizon.
Of course, you can operated the turbines singly for a mere 200hp to maintain a positively pedestrian 150mph.
Or you can engage both turbines for full power and maintain speeds in excess of 200mph!
Micro Turbines that work
The main problem with gas turbine engines is scaling them down to the size useful in a car.
This is due to the close tolerances required for efficient use.
In the Impulse-EV this problem is removed by the use of centrifugal scrolls used in turbine superchargers instead of the axial fan turbines used in aircraft.
To attain the high compression ratio needed the engine uses multiple centrifugal compressor stages in series each stage multiplying the ratio of the previous.
These are decoupled from the turbines so will maintain high compression at all speeds.
In the car the first-stage compressors are located at the front of the car.
The partially compressed air is then ducted via a heat exchanger to the remaining compressors at the rear.
This is possible due to the decoupling of the compressors and turbines.
Large high extract heat exchangers
The heat exchangers extract heat from the engine exhaust to pre-heat for the later stage compressor.
This will extract almost all the exhaust heat since the heat exchangers are about 2 metres long.
The exhaust will be no warmer than current small piston engine exhaust.
This is possible due to the long duct between the compressor stages.
Links:
Hybrid turbocharger |
Design and development of an advanced two-stage centrifugal compressor |
LHTEC T800
Production of ceramic turbine components by electrical discharge machining |
T800 Helicopter Engine |
Turbokart TURBINE PROJECTS
Ceramics for turbine engines |
Turbokart LHTEC T800-LHT-801 |
hvwc Black Current III |
Gas Turbine Project Pages